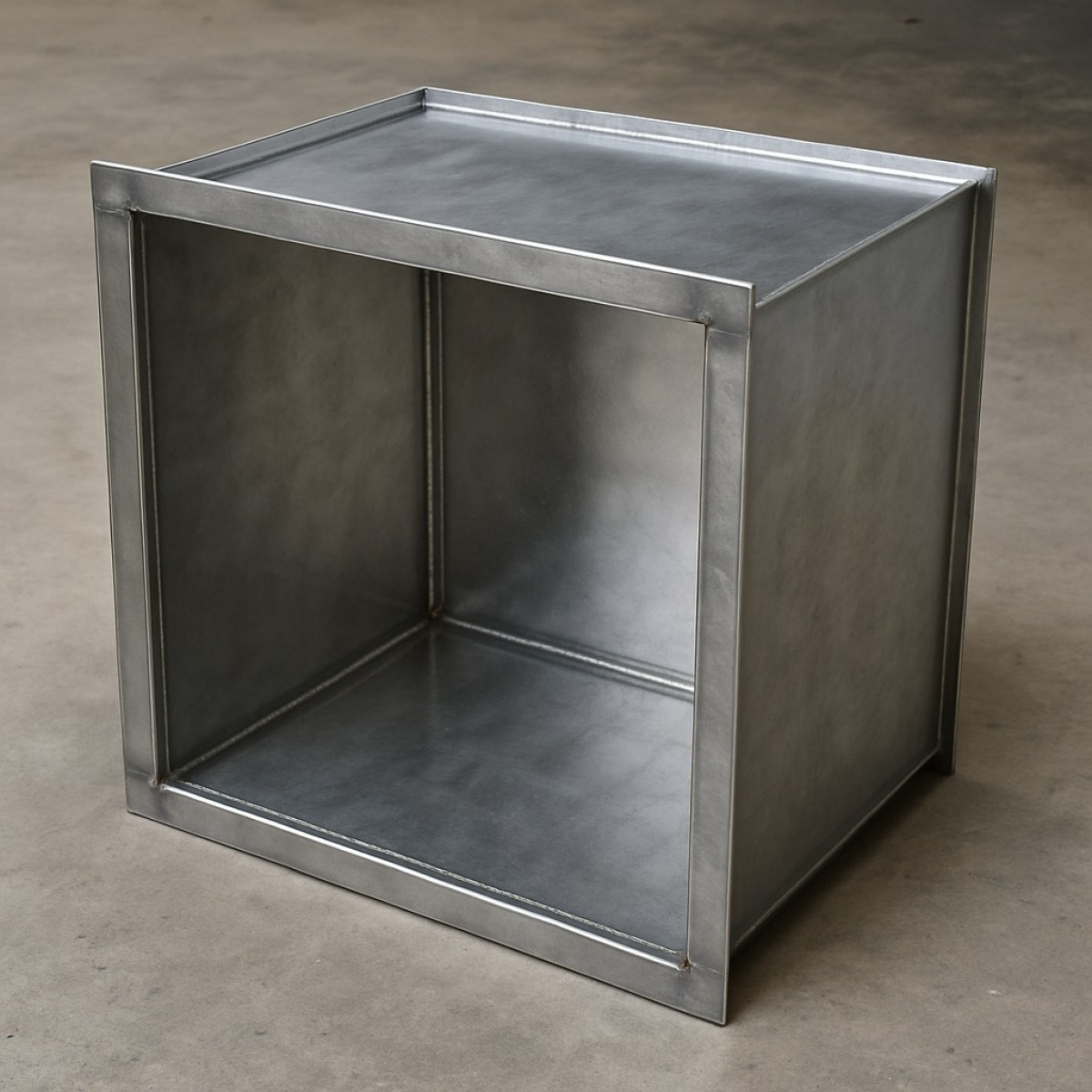
- Model: SS-316-SQ-DUCT
- Weight: 20.00kg
- Dimensions: 1,000.00mm x 150.00mm x 150.00mm
316 Stainless Ductwork for corrosive environments
Pharmaceutical Manufacturing
Handling airborne solvent vapors, corrosive powders, or fumes.
Cleanroom compatibility.
Chemical Processing Facilities
Extracting or conveying acidic, toxic, or highly reactive gases.
Suitable for fume cupboards and reactor extract systems.
Laboratories (Biological & Chemical)
Ducting for fume hoods with high chemical exposure.
Ensures long-term integrity with minimal degradation.
Waste Incineration and Wastewater Treatment Plants
Corrosive off-gas extraction.
Hydrogen sulfide and other aggressive compounds are common.
Food Processing Plants (Aggressive Cleaning Agents)
Environments where strong chlorinated or acidic cleaners are used.
Aerospace or Electronics Facilities
Where clean, contamination-free exhaust air systems are critical.
Why It’s Necessary
Corrosion Resistance: 316 includes molybdenum, which significantly improves resistance to chlorides, acids, and industrial solvents.
Longevity: Stainless systems don’t degrade like galvanized or aluminium under chemical stress.
Safety: Prevents duct degradation that could leak hazardous fumes into occupied spaces.
Compliance: Enables installations to meet strict air quality, environmental, and fire safety regulations.
DW/144 Guidance Highlights (Relevant to Stainless Steel)
DW/144 is primarily written for galvanized mild steel, but when using alternative materials like stainless steel, you should:
Material Specification:
Declare material in job specs and on drawings. State “316 Stainless Steel to ASTM A240”.
Ensure proper gauge for the duct size and pressure class.
Welding & Joints:
Seam welding is recommended in corrosive environments.
Fully seam-welded ductwork (longitudinal and transverse) prevents corrosion in crevices.
Use TIG or laser welding for neat, low-contamination seams.
Testing Requirements:
DW/144 recommends pressure/leak testing for high-integrity systems — mandatory if toxic gases are present.
Consider hydrostatic or dye penetrant testing on welds if it’s safety-critical.
Should It Be Fully Seam Welded?
✅ Yes, for toxic or aggressive environments.
Reasoning:
Seam welding avoids pinholes or gaps where corrosion could start.
Eliminates reliance on mastic or gaskets, which may degrade under chemical exposure.
Offers maximum integrity for high-pressure or hazardous airflows.
Needed for compliance with higher safety standards, e.g. ATEX or hazardous exhaust systems.